Why new technology is the future of the construction industry
The construction industry faces many challenges. New technologies from augmented reality and digitisation to exoskeletons and robotics can help solve them. Matthew Partridge reports.
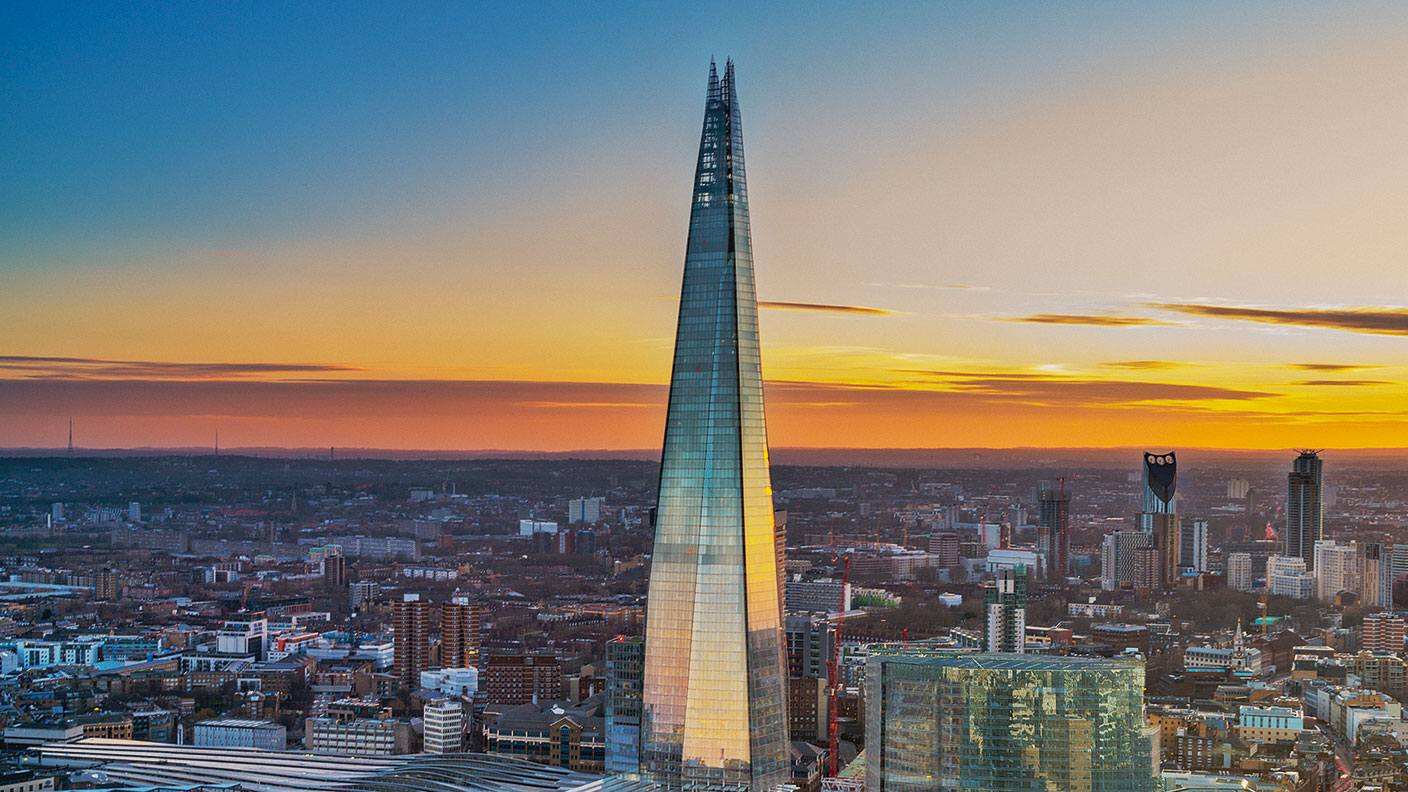
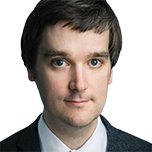
The construction industry is booming. From houses to motorways, demand has never been higher. But while demand has increased, productivity hasn’t. The productivity of workers in the two decades up until 2017 increased by just 1% per year, compared with 2.8% for the global economy and 3.6% for manufacturing, according to consultancy McKinsey.
With long-term labour shortages looming, there are big opportunities to improve the way the industry works. Construction is facing four major challenges, says Russell Haworth, chief executive of construction technology platform NBS.
First, there is an increased emphasis on safety. Second, there has been a big jump in the quality of building that people expect. Environmental sustainability is also a hot topic as governments talk of trying to cut net carbon emissions to zero. Finally, the industry is facing staff shortages and attempts to recruit a new generation of workers are running into construction’s reputation for the “three Ds”: dirty, dull and dangerous. Many of these issues can be tackled through better use of technology.
Subscribe to MoneyWeek
Subscribe to MoneyWeek today and get your first six magazine issues absolutely FREE
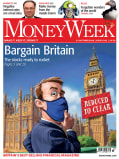
Sign up to Money Morning
Don't miss the latest investment and personal finances news, market analysis, plus money-saving tips with our free twice-daily newsletter
Don't miss the latest investment and personal finances news, market analysis, plus money-saving tips with our free twice-daily newsletter
Cutting out the paperwork
The first major innovation is digitisation. Almost every construction project goes through several stages: coming up with the original idea; drawing up the designs; preparing the construction; execution and building; operation and maintenance; and finally demolition and recycling. Manufacturers are also involved in building everything from windows to fireretardant systems. Up until recently plans for each stage of the project were drawn up with pen and paper, and the process still largely involves people in various parts of the supply chain sending separate files to each other.
This creates a huge amount of paperwork, which makes it hard to make changes if problems emerge and slows down communication between different parts of the supply chain. Having all the data on a single digital platform reduces the amount of paperwork, compared with pen and paper, or even individual digital files, and also allows those at various stages of construction to communicate more efficiently, says Haworth.
For example, designers “can specify a building that meets safety codes at an early stage of development”, with manufactures “immediately starting to build components that meet these requirements”. The benefits of digitisation don’t stop there, says Jonathan Hunter, chief executive of software company Eleco.
Software such as that made by his company – which has been used in projects ranging from the Shard to the London Eye and the redevelopment of the V&A Museum in London – can help speed up the pace of construction.
This is because sharing of data between contractors on a project allows firms to monitor progress in real time, “adjusting their schedules according to how it is developing”, so if there is a delay in the project “the manager can add extra resources”. What’s more, digitisation can also help designers to create more efficient and sustainable buildings, by allowing them to make better estimates of a building’s costs over its lifespan, says Hunter. Both factors are “increasingly important these days”: not only do buildings with green credentials “attract higher rents”, but there is also now a general recognition that operational costs, rather than upfront expenses, are the most important factor in determining the viability of a project. Studies show that when you look at the total cost over a building’s lifespan, 85% “is in the operation, with construction accounting for only 15%”, he says.
With digital technology reaching the point “where an entire project-management platform can be put on an app”, digitisation is about to reach a tipping point where it begins to be widely adopted, say Ibrahim Imam and Sander van de Rijdt, the founders of construction project-management software company PlanRadar.
They already have 16,000 clients using their software, but they think that this is just a “drop on a hot stone” compared with the huge potential demand for digital technology. “Up to 2.5 million companies around the world could benefit from this technology.”
Improving accuracy with augmented reality
Digital project management may be just the first step in the construction technology revolution. The use of augmented reality (AR) “is still in its pilot phase”, but has long-term potential, say Imam and van de Rijdt. AR is similar to virtual reality, in that it involves immersing people in computer-generated reality via special goggles or a headset. However, rather than completely replacing the physical reality, augmented reality combines the two, “so you can overlay the real-world plans with computer graphics and compare the two”. XYZ Reality is already developing tools for applying AR technology to construction. Its system allows those working on construction sites essentially to “view holograms of the building to millimetre accuracy”, says XYZ’s founder David Mitchell.
This allows engineers and builders to visualise where buildings, structures and fittings should be placed, and to check if they have been built correctly. Crucially, AR also ensures builders “build things right the first time” – something existing technologies, such as laser tools, are unable to facilitate. This last point is important since inaccuracy and waste is an Achilles heel for the construction industry, says Mitchell.
He notes that 80% of construction works are built to a degree of inaccuracy that is out of engineering tolerance, with 10% built so badly that they have to be redone. This reworking is environmentally unfriendly – in terms of waste and carbon emissions – costly and time consuming. He claims that his customers have been able to cut the amount of reworking required from 10% to 1%, saving them around nine times the cost of the system.
Changing data, changing plans
Digitisation and AR can help ensure that all parts of the construction supply chain follow the plan, but what if the plan itself needs to be changed? At the moment most building plans “are quite static, in that it’s hard to change them”, says Juan de Dios Hermosín Ramos of technology and engineering firm Ayesa.
However, even the best plans and designs could always do with some tweaking in light of an unexpected development or feedback. As a result, the next major area of innovation will be in “dynamic modelling”, he says. In essence, this is where the plans are adjusted in light of the new data. Until now, this has been very difficult to do.
But the combination of cheap sensors with digitisation means that it should become increasingly common for all those involved in a project to receive a huge amount of data, giving them an indication of emerging problems. Consider the example of a building that starts to vibrate because of a flaw, or something that the architects didn’t anticipate, such as wind, says Hermosín.
This might only be detected years after the building was constructed, by which point fixing it could become extremely expensive. With sensor technology “such vibrations could be picked up at an early stage of the project, alerting those involved that the design needs to be changed”.
The idea of information flowing from the building or infrastructure “is still in its early stages, and expensive to implement”. However, with the industry as a whole “much more open to using technology”, we can expect “some quite radical changes in this direction over the next two to three years”, creating “big opportunities” for companies in this area.
Robots and humans working together
One reason why construction has failed to keep pace with the gains in productivity experienced by manufacturing is because it is “one of the least roboticised industries”, says Kevin Albert of robotics firms Canvas. It is no coincidence that productivity took off in manufacturing and logistics during the 1980s, “the same period when industrial robots started to enter the mainstream”, he argues. Implementing robotics in these sectors was simpler: “while industrial environments are standardised and certain, every building is different”.
But developments in sensors mean that it is increasingly possible to automate “dynamic and uncertain” environments, such as building sites. A case in point is Canvas’s own robots, which focus on drywall finishing in buildings. While this may seem a niche area, it is very labour intensive, “incredibly physically tough” on workers who have to prepare the paint and then apply and sand it, and has a tendency to “create bottlenecks” in the building process.
By automating parts of the process, the robots can “cut the time needed from five to seven days to just two”, while allowing humans to focus on directing the robots and fine-tuning the application of paint. This makes the job safer and more interesting, especially to younger workers who feel that the “tools, skills and career path in construction doesn’t speak to them”.
The idea of robots and humans working together will transform construction, says Kim Povlsen of Universal Robots. Traditionally, robots have been seen as “something dangerous” that “needs be locked away in cages or behind glass screens”. In the not so distant future they are likely to be smaller, run from batteries and mounted on wheels, making them much more mobile than their cousins in factories.
Combined with making them easier to program, this should allow them to be brought on site and adapted to specific conditions.
This approach is reflected in how Universal Robots operates. Rather than build dedicated robots for each task, it has designed the basic hardware in a way that individual companies – such as Canvas, which uses its robots – can modify and customise as efficiently as possible. This is “still relatively new”, but Povlsen is optimistic. With the construction industry “becoming much more open to using robots”, we have “only seen the tip of the iceberg in terms of what robots can do”, he says.
Adding support with exoskeletons
We can also improve what humans can do by using exoskeletons – wearable machines that support and protect the user. By reducing the pressure on the body, they “can play a huge role to improve the health and safety of site workers”, says Graeme Larsen, associate dean of sustainability at University College of Estate Management and a visiting professor at RMIT University. They have the potential to enable construction workers to “work longer, be less fatigued, have less sick days, avoid injury, and be able to do manual work into later life without adversely affecting their body”.
There is a growing amount of evidence to back this up, says Michiel de Looze of TNO Netherlands, which focuses on applied scientific research. A study last year looked at a group of plasterers who were offered the use of exoskeletons to help with their job. Far from being resistant to the devices, the plasterers, who spent a large part of their job working with their hands above their head, found the exoskeletons useful.
Over 90% of those who took part in the study felt that the exoskeletons provided additional support and half of them reported feeling less tired at the end of the day. The industry is fast approaching a “turning point” in the adoption of exoskeletons, with a “definite increase” in the numbers used, says de Looze. This is particularly noticeable in some of the most physically demanding and repetitive jobs – they are “less useful in more dynamic jobs that involve a greater degree of movement and flexibility”.
Exoskeletons are now starting to move from very basic ones based around springs to those that use motors (known as actuators) to adjust the level of support that they provide. “There is both a greater awareness and a higher level of acceptance of assistive technologies in the construction industry,” agree Jason Jones of exoskeleton firm Ekso Bionics and William Shaw, a senior adviser to the firm.
For example, firms are increasingly turning to exoskeletons to help them broaden the construction workforce to include workers who are older, smaller, or less physically strong. The type of devices are also becoming more sophisticated and may soon be able to be used to stack and pick up materials, tasks they were previously unsuitable for. Ultimately, the benefits of exoskeletons may be so great that in the long run they could become a form of personal protective equipment, says Larsen. T
his is unlikely to happen quickly – adoption “is a complex process involving a range of stakeholders” – but they could eventually be mandatory for certain tasks, just like the now-ubiquitous hard hat.
Get the latest financial news, insights and expert analysis from our award-winning MoneyWeek team, to help you understand what really matters when it comes to your finances.
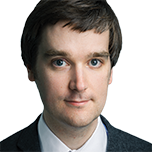
Matthew graduated from the University of Durham in 2004; he then gained an MSc, followed by a PhD at the London School of Economics.
He has previously written for a wide range of publications, including the Guardian and the Economist, and also helped to run a newsletter on terrorism. He has spent time at Lehman Brothers, Citigroup and the consultancy Lombard Street Research.
Matthew is the author of Superinvestors: Lessons from the greatest investors in history, published by Harriman House, which has been translated into several languages. His second book, Investing Explained: The Accessible Guide to Building an Investment Portfolio, is published by Kogan Page.
As senior writer, he writes the shares and politics & economics pages, as well as weekly Blowing It and Great Frauds in History columns He also writes a fortnightly reviews page and trading tips, as well as regular cover stories and multi-page investment focus features.
Follow Matthew on Twitter: @DrMatthewPartri
-
Divorced? Simple rules to stop your ex claiming inheritance on your estate
Divorces are back at pre-pandemic levels leaving lawyers urging separated couples to get their affairs watertight to avoid any nasty disputes after death
-
Is now a good time to invest in Europe?
European stocks are undervalued, but experts believe that defence and infrastructure spending could see renewed growth
-
How Trump's dog deals will damage global trade with the US
Opinion Some commentators are hailing Trump’s trading savvy. Are they right?
-
Emerging markets must deliver growth
Emerging markets have benefitted from the rotation away from the US – but can the rally last?
-
Global equities that should prove resilient to the stock market’s storms
Opinion Alex Illingworth of Goshawk Asset Management highlights three diverse opportunities in global equities despite a turbulent landscape
-
Philip Coggan: 'Donald Trump means business on tariffs'
Interview What could Trump's tariffs mean for the US and global economies? Philip Coggan, former columnist at the Financial Times and The Economist, explains
-
Will the global boom in defence spending drive economic growth?
Defence spending is soaring, and politicians in the UK and Europe are telling voters it will be a major boost to economic growth. But is that really the case?
-
The true nature of economic growth
Opinion The feds making a number go up is one thing; true economic growth is quite another, says Bill Bonner
-
'Capitalism is suffering death by a thousand cuts': Ruchir Sharma talks to MoneyWeek
Interview Ruchir Sharma, author of What Went Wrong with Capitalism, explains how free enterprise in developed economies has been undermined by continual state interference
-
Israel claims victory in the '12-day war' with Iran
Donald Trump may have announced a ceasefire in the 12-day war between Israel and Iran, but what comes next depends on what happens internally in Iran