How to invest in smart factories as the “fourth industrial revolution” arrives
Exciting new technologies and trends are coming together to change the face of manufacturing. Matthew Partridge looks at the companies that will drive the fourth industrial revolution.

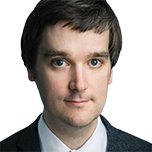
We’ve all heard in school about the first industrial revolution and how the steam age transformed the world. The mass adoption of electricity that began in the late 19th century ushered in the beginnings of mass production, while after World War II, automation, robotics and computers further transformed the way things were made. Now, another wave of big change is sweeping industry. Whether you call it the “fourth industrial revolution”, “industry 4.0” or “smart manufacturing”, this evolution is set to power a new era of growth.
The best way to sum up the fourth industrial revolution is as “the coming of age of technologies developed during the last two decades”, says Mark Yeeles, who heads the industrial automation business at Schneider Electric. While many of these technologies may have been around in some form for several years, their development has now reached the point where they are so cost-efficient that they are starting to move from the research laboratory to the factory floor. In short, it is the “coming together of people, culture and technology to solve sophisticated challenges”.
Industry is being changed by a “wave of new technologies” that are “showing great promise in industrial applications”, adds Peter Lingen from the robotics team at investment manager Pictet. However, what makes them truly revolutionary is the fact that they don’t just have great potential on their own, but they can also be used together “to improve the way that we produce things”. Digitalisation, automation and other trends are finally making the idea of a “smart factory” – long a dream of many engineers and industrial scientists – a reality, he says.
MoneyWeek
Subscribe to MoneyWeek today and get your first six magazine issues absolutely FREE
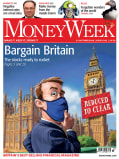
Sign up to Money Morning
Don't miss the latest investment and personal finances news, market analysis, plus money-saving tips with our free twice-daily newsletter
Don't miss the latest investment and personal finances news, market analysis, plus money-saving tips with our free twice-daily newsletter
That’s why companies are not simply talking about smart manufacturing, but are also starting to spend increasingly large sums on the technologies behind it, says Joel Tortolero, chief executive of Wikifactory, an online platform for linking designers, engineers and manufacturers. Broadly defined, the market is already worth hundreds of billions, with one estimate putting current spending at roughly $280bn per year worldwide, he says. This is set to increase in the next few years – demand “is growing by around 20%-25% each year” and projections suggest it could reach $455bn by 2025 and $600bn by the end of the decade.
Digitalisation
The first pillar of the smart-manufacturing revolution is the use of digital technology. One part of this is the increase in use of online platforms, such as Wikifactory, to design and manufacture goods. At the most basic level these platforms “allow companies to keep track of their designs as they evolve, rather than have changes buried in an avalanche of emails and separate documents”, says Tortolero. This in turn makes it easier for companies to collaborate with suppliers and customers to make changes quickly based on feedback, “cutting down on wastage and carbon emissions”. Over the past two years, Wikifactory has grown from 79,000 to 136,000 users, with 9,000 physical products currently being developed.
Manufacturing platforms are important, but they aren’t the only aspect of digitalisation that is changing the way that we make things. Another key aspect is the collection of much larger amounts of data on every aspect of production. When it comes to smart manufacturing, “the data is just as important as the machines that do the actual production”, says Michael Colarossi, who oversees products and innovation in retail branding and information solutions for Avery Dennison, a labelling and packaging specialist.
Advances in data collection – especially around sensor technology and intelligent labels (labels that come with tracking devices or other technology embedded within them) – mean that “hundreds, if not thousands of variables” can now be collected at relatively low cost. This data collection doesn’t have to stop once the product leaves the factory. For example, intelligent labels could be used by a fashion company to tell them when demand for a particular garment is rising, leading them to increase production. He thinks that such labels will become an important part of supply-chain management for all types of manufacturers.
Artificial intelligence
Collecting the data is only half the challenge. The next is to use it to produce tangible gains in performance and efficiency. The good news is that this has never been easier, as artificial intelligence (AI) “is improving, in both the speed and the quality of the tasks it can perform”, says Colarossi. For example, AI is helping firms “get much better at using historical data to predict the future success of products”.
“Artificial intelligence can definitely help firms understand the market, including forecasting demand,” agrees Phani Bhushan Sistu, who leads the “internet of things” solutions at IT group Hitachi Vantara. It can also be used to help firms get the most from their equipment, including seeing how their machines can best be optimised over their life cycle and when they are most likely to break down, helping firms avoid delays and production bottlenecks. This is especially true in an age when robots and other devices in factories are expected to communicate with each other.
AI is also been increasingly used in quality assurance, notes Sistu. Until recently, product checks were traditionally carried out by humans at the last stage of the production process, just before goods were ready to ship. However, many factories now use AI-based imaging systems. Not only can they find defects in products more efficiently and quickly than their human counterparts, but they can do so at a much earlier stage. This allows the problem to be tackled at the point where it emerges, rather than having to disassemble the whole production line.
Using AI to analyse data is certainly a big advance, but even this may not prove to be the limit of how it can be used to improve manufacturing as the ability of machines to act autonomously develops. Some machines in factories are so sophisticated that they can not only flag up problems using critical data, but also “make quick decisions about how to deal with them”, for instance by adjusting the way in which they operate, without the need for further human intervention, says Yeeles.
Computers are even playing an increasing role in research and development – traditionally seen as the one job that was too intelligent for them. While human beings will still come up with the initial ideas and make the final decisions, computing advances mean that much of the trial and error that occurs in the middle of the process is increasingly being automated. Computers are proving particularly good at tweaking designs and then simulating them to make sure they are optimised. This both improves performance and speeds up the design process.
Additive manufacturing
The past few years have also seen major advances in additive manufacturing – the name for processes that make products by adding layers of material, such as 3D-printing. Because you don’t have to build a new mould every time you change a design, additive manufacturing “gives you a lot more freedom and flexibility in how you design a component”, says Nigel Robinson of the Digital Manufacturing Centre in Silverstone, a venture set up by engineering consultancy KW Special Projects. Indeed, “certain advanced design techniques, such as honeycombing and lattice structures, are only possible using additive manufacturing”.
Still, additive manufacturing isn’t without its flaws. For one thing, there are limits on the type of materials that can be manufactured in this way. Traditional techniques have also been much more cost-efficient when it came to producing large numbers of components. As a result, firms would typically just use 3D-printing for producing prototypes. But this is changing, as recent advances mean that the “range of material choices have vastly improved”, while the costs have come down, which is why it is increasingly being used to make the final product in industries such as aerospace, as well as in parts of the medical and oil and gas industries.
A case in point is the car industry. Initially, additive manufacturing was only economic for Formula One teams that “were willing to pay any price for the relatively small gains in performance that come from small quantities of customised components”, says Robinson. As the cost of the process has come down, it is moving down the value chain, and is increasingly used by firms making ultra-expensive hypercars, who typically produce runs of around 100-300 cars, as well as some makers of sports cars. He thinks that within a decade components produced by additive manufacturing will routinely appear in family cars.
Distributed manufacturing
The past few years have also seen the rise of distributed manufacturing. Until recently, manufacturers offshored their production to emerging markets, taking advantage of low wages, before shipping them to consumers around the world. However, this model has proved vulnerable to various “systematic shocks”, says Bart Van der Schueren, chief technology officer at 3D-printing specialist Materialise. These include China’s harsh zero-Covid policy, which has shut down factories and led to global shortages of key components, the temporary blockage of the Suez Canal by a container ship and Russia’s invasion of Ukraine. Growing recognition of the carbon emissions from transport is also disrupting global manufacturing.
What’s more, decades of rising wages in emerging markets mean those markets no longer have a large cost advantage over the developed world, especially in industries that are more capital intensive, adds Lingen. Thus “entire supply chains are likely to become increasingly regional in the coming years” as companies move production closer to consumers. We should also see more investment in advanced automation.
Of course, the idea of moving from one centralised large factory to several smaller factories that are geographically separated comes with its own risks. Above all, companies “want to ensure that all their components have the same quality, irrespective of where they are produced”, says Van der Schueren. But he’s confident that companies can harness additive manufacturing to help them meet the challenge of making smaller individual batches of high-quality components. Indeed, distributed manufacturing could end up being a positive strategy in its own right rather than just a response to problems with global supply chains, if companies combine big data and artificial intelligence with the flexibility of additive manufacturing to “produce localised products that are tailored to the needs of customers in a specific area”.
Bringing it all together
Hypercar manufacturer Czinger epitomises the fourth industrial revolution. It uses what it describes as its own three-part digitalised “divergent adaptive production systems” (DAPS) to build and manufacture its vehicles. Czinger’s designers come up with a list of criteria, such as performance, ease of manufacturing and cost control, that each of the car’s components need to meet. They then run it through an AI-driven system that uses machine learning automatically to generate, and then simulate, various component designs “until it has generated a design that perfectly matches the input constraints”, says Kevin Czinger, the founder and chief executive. These super-optimised components are made using additive manufacturing, then put together using a universal assembler that can put together any set of 3D-printed components “in a fully automated, fixture-less way”. All of this is done at Czinger’s headquarters in Los Angeles, close to where most of the customers for its $2m 21C car live.
Czinger argues that his company’s use of smart manufacturing has allowed it to benefit from “low production capital requirements and a fast product cycle”. In the next few decades, “we will have full digitisation of manufacturing processes, regionalisation or localisation (on a global basis) of the design and manufacture of most products, and the global democratisation of access to the tools of product design and creation”, he says. In the box below, we look at some of the stocks that could benefit from this.
Five smart-manufacturing stocks
PTC (Nasdaq: PTC) provides a range of software and services for manufacturing companies focused on the internet of things and collaborative software, as well as advanced data analytics, automation and augmented reality. Revenue has grown by roughly 10% a year since 2016, while profits have grown more than 60-fold since 2017, with a double-digit return on capital employed (ROCE). At the current share price of $125, it trades on 24 times forecast 2023 earnings.
Schneider Electric (Paris: SU) specialises in energy management and industrial automation, and its products should play a key role in smart factories. The group operates in 200 locations around the world and collaborates with a wide range of companies, including Cisco and Microsoft. Schneider’s profits grew by 70% between 2016 and 2021 and are set to keep rising, and it manages a ROCE of around 10%. At €136, it trades at 17.4 times 2023 earnings. The dividend has grown at more than 7% per year over the past five years and the trailing yield is 2.2%.
Industrial and engineering firm Siemens (Frankfurt: SIE) is also closely involved in the development of smart manufacturing. The company is a “powerhouse” when it comes to automation technology, says Peter Lingen of Pictet. Its digital business platform Siemens Xcelerator is also regarded as one of the leading products in this area. While its products and services related to the fourth industrial revolution still only account for roughly 15% of revenue, they are growing by about 10% a year, which means that this part of the business will become much more important in the future. Siemens trades at 13 times 2023 earnings with a dividend of 3.6%, based on a share price of €112.
Rockwell Automation (NYSE: ROK) specialises in many goods and services that are used in industrial automation. Its products range from those that collect data to visualisation software and even systems that can automate entire processes. Sales growth has been solid and the backlog of orders is rising. The company is also very profitable, with operating margins averaging 17% over five years and a ROCE averaging 22%. Earnings per share doubled between 2015 and 2021. A share price of $260 puts it on 23.5 times 2023 earnings and a yield of 1.7%. The dividend has grown by 8% per year over the past five years.
Proto Labs (NYSE: PRLB), founded in 1999 by entrepreneur Larry Lukis, is one of the world’s leading producers of custom prototypes and low-volume production parts. It operates in eight countries in North America, Europe and Asia. After originally focusing on injection moulding, it started to embrace 3D-printing in 2014, and now provides five different types of additive processes. Last year it acquired 3D Hubs, a digital-manufacturing platform that incorporates machine learning. Proto Labs serves a large number of companies in the medical, aerospace, automotive, consumer electronics and industrial equipment sectors. It has grown sales by roughly 10% per year over the past five years. A share price of $46 puts it on 23.6 times 2023 earnings.
Get the latest financial news, insights and expert analysis from our award-winning MoneyWeek team, to help you understand what really matters when it comes to your finances.
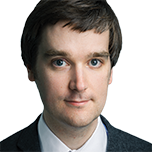
Matthew graduated from the University of Durham in 2004; he then gained an MSc, followed by a PhD at the London School of Economics.
He has previously written for a wide range of publications, including the Guardian and the Economist, and also helped to run a newsletter on terrorism. He has spent time at Lehman Brothers, Citigroup and the consultancy Lombard Street Research.
Matthew is the author of Superinvestors: Lessons from the greatest investors in history, published by Harriman House, which has been translated into several languages. His second book, Investing Explained: The Accessible Guide to Building an Investment Portfolio, is published by Kogan Page.
As senior writer, he writes the shares and politics & economics pages, as well as weekly Blowing It and Great Frauds in History columns He also writes a fortnightly reviews page and trading tips, as well as regular cover stories and multi-page investment focus features.
Follow Matthew on Twitter: @DrMatthewPartri
-
What is the 25x retirement rule and does it work?
The 25x retirement rule has been around for decades but many experts question if it is a suitable strategy
-
When is the self-assessment tax return deadline?
If you are self-employed, rent out a property or earn income from savings or investments, you may need to complete a self-assessment tax return. We run through the deadlines you need to know about
-
Halifax: House price slump continues as prices slide for the sixth consecutive month
UK house prices fell again in September as buyers returned, but the slowdown was not as fast as anticipated, latest Halifax data shows. Where are house prices falling the most?
-
Rents hit a record high - but is the opportunity for buy-to-let investors still strong?
UK rent prices have hit a record high with the average hitting over £1,200 a month says Rightmove. Are there still opportunities in buy-to-let?
-
Pension savers turn to gold investments
Investors are racing to buy gold to protect their pensions from a stock market correction and high inflation, experts say
-
Where to find the best returns from student accommodation
Student accommodation can be a lucrative investment if you know where to look.
-
The world’s best bargain stocks
Searching for bargain stocks with Alec Cutler of the Orbis Global Balanced Fund, who tells Andrew Van Sickle which sectors are being overlooked.
-
Revealed: the cheapest cities to own a home in Britain
New research reveals the cheapest cities to own a home, taking account of mortgage payments, utility bills and council tax
-
UK recession: How to protect your portfolio
As the UK recession is confirmed, we look at ways to protect your wealth.
-
Buy-to-let returns fall 59% amid higher mortgage rates
Buy-to-let returns are slumping as the cost of borrowing spirals.