3D printing: a blueprint for the future of manufacturing
Five years ago, 3D printing was a bubble that burst. But now its time has finally come – and its successor technology, 4D printing, is on the horizon, says Matthew Partridge.
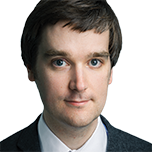
Investing in new technology tends to follow a set pattern. First you have a period where the technology languishes in obscurity. Next you have an explosion of interest, turning into hype. However, when it becomes clear that the technology will take longer than initially expected to develop and go mainstream, there is a collapse in interest between 2012 and 2014 shares in companies related to 3D printing soared before falling back over the next two years.
Finally, when everyone's attention is elsewhere, the technology begins to deliver on its promises. The trick, then, is to buy after the bubble has popped and everyone is too traumatised or sceptical to jump back in. Three-dimensional (3D) printing is currently in this position.
Transforming production
The best way to understand 3D printing, and its benefits, is by contrasting it with traditional manufacturing. Until recently, "companies made things in one of two ways: either by carving and shaping blocks of raw materials, or by injecting or pouring liquid materials into a mould", says Peter Leys, executive chairman of Materialise, which has been involved with 3D printing for nearly three decades. While both processes, particularly moulding, "are very good if you want to produce large numbers of identical objects very quickly at a low cost", making even minor changes to the objects requires resetting entire production lines and creating new moulds, a time-consuming process.
Subscribe to MoneyWeek
Subscribe to MoneyWeek today and get your first six magazine issues absolutely FREE
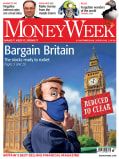
Sign up to Money Morning
Don't miss the latest investment and personal finances news, market analysis, plus money-saving tips with our free twice-daily newsletter
Don't miss the latest investment and personal finances news, market analysis, plus money-saving tips with our free twice-daily newsletter
By contrast, 3D printing is a sophisticated form of manufacturing using specialised equipment, known as 3D printers, to create objects from a digital design by adding together a large number of very small layers of material, some as small as 0.1 millimetres. So an object is essentially created from the bottom up, slice by slice. This means that if you want to change the way something looks, instead of setting and resetting production lines, you can just alter the digital image that is sent to the printer, "drastically cutting the time needed to produce new models", says Leys.
It can also affect the production process in other ways. For example, "because it is as easy to print 16 variations of a single design as it is to produce 16 copies of one design", it can make it much easier for firms to focus on producing copies of a product tailored to the individual customer. Objects that can now be 3D-printed range from guitars and guns to medical dummies and engine components.
A big boost to productivity
3D printing also improves productivity by allowing increased complexity. Traditionally complex products had to be split up into several different parts, which were then put together during the assembly process. Because this can be expensive and time-consuming, designers and engineers "are taught... to keep designs as simple as possible in order to make them easier to manufacture", says Leys, even if this involves compromising on other aspects, such as quality. However, because the 3D-printing process involves creating entire objects in one go, designers can now concentrate on quality "without having to deal with artificial constraints around complexity".
These advantages meant that when 3D printing was first developed in the late 1980s firms used it in order to help them create prototypes quickly. For a time 3D printing was known as "rapid prototyping". Even today this remains a major application for the technology, with companies sending designs on the Monday to the likes of Materialise, "which deliver the prototype the next day, to be tested on the Wednesday, revised and resent on Thursday", says Leys. This leads to the finished product "being delivered on the Friday, so that the firm can start to set up production lines for moulding".
However, while speedily producing accurate prototypes is an important function, the real breakthrough in the technology came around a decade ago when engineers began to realise that "it's more efficient to use 3D printing for the end product as well, rather than just using it to create prototypes", says Leys. This is particularly the case for products that "involve complex designs, or where an additional degree of personalisation could make them much more effective".
A vast range of applications
The advent of widespread 3D printing "is an excellent example of how a technology moves along the Gartner Hype Cycle from what we call its Innovation Trigger point toward widespread use on the Plateau of Productivity", says Pete Basiliere of research and advisory firm Gartner. Indeed, 3D printing has become so established in certain areas, such as the manufacture of hearing aids, that Gartner no longer bothers to track its use for those purposes, instead looking at other potential applications.
At present 3D printing is widely used in the medical sector, especially in the production of implants, and the aerospace industry, where it helps make engines and turbines more efficient, says Mikael Schuisky, vice president and head of research, development and operations at Sandvik, a Swedish engineering firm. However, other industries are also queuing up to incorporate 3D printing into their supply chains.
This includes everyone from railway companies and oil and gas firms, who are using it to produce parts used in drills and nozzles, to footwear makers, with Nike and Under Armour incorporating 3D-printed products (mainly plastics) into their shoes. Based on his experience at Sandvik, Schuisky expects demand for 3D printing to grow at around 20%-25% a year for the next five years before the industry starts to mature.
Hewlett Packard (HP) is also experiencing furious growth in demand for its 3D printers and printing materials. For example, its printers have enabled prosthetics firms to "revolutionise their products", and Volkswagen, GKN and BMW to "evolve automotive mass production", while Bowman International is also using its printing materials to "produce robust, cost-effective construction products", according to George Brasher, HP's UK managing director. In addition to helping other companies take advantage of the 3D-printing revolution, HP is incorporating it into its own production processes. It has used 3D printing to slash the cost of some key components in its own printers by as much as 95%, while reducing the weight of the parts by 90%.
DIY: 3D printing at home
Even home printing is managing to find a niche, albeit a smaller one than many people predicted five years ago. Chengxi Wang, the chief executive of 3D-printing platform MyMiniFactory, notes that the number of unique users on her firm's systems is now more than 500,000 each month, with "over one million items downloaded and 3D printed each quarter".
This is being supported by a "growing community of more than 14,000 3D designers uploading more than 700,000 of their designs to the platform". With the cheapest desktop 3D printer now available for just £300, she expects sales of desktop printers "to increase rapidly to over two million units this year". Popular items range from toy Star Wars figures to fan-grill covers.
Schuisky and Wang may seem optimistic, but their projections are in line with those of other analysts. The market research firm Wohlers Associates has been tracking the growth of the 3D-printing industry closely, and its latest report forecasts that total revenues will grow to nearly $16bn (£13bn) in 2020 for all products and services related to 3D printing. This should rise to $35.6bn by 2024, roughly in line with the rate of growth expected by Schuisky. Overall, it expects "many new players, hundreds of millions of dollars invested, and innovative new products designed", driven by machines that "can produce objects of much better quality and at a faster speed than they could five years ago".
4D printing: the new cutting edge
Demand for 3D printers and related technology is growing at a tremendous rate as the technology starts to enter the mainstream, with at least a decade of strong growth yet to come. However, its place on the real cutting edge of technology has been eclipsed by 4D printing, a concept attracting a large amount of attention from researchers and some corporations. The best way to describe 4D printing is to imagine that it's akin to "using 3D printing to construct multi-material objects that can subsequently transform themselves", says Professor Skylar Tibbits, the founder and director of the Self-Assembly Lab at the Massachusetts Institute of Technology (MIT).
Tibbits points out that the idea of using materials to create objects designed to evolve with their surroundings "has been around for centuries", with both winemakers and early shipbuilders "taking advantage of the fact that wood absorbs moisture when it's hot and expels it when it get cold". Unfortunately, "a lot of this knowledge was overlooked when manufacturing shifted from craft production to mass production, since it proved simpler to just print one static structure". This has created a lot of inefficiencies. For example, if you want to change the amount of water flowing through water pipes, you either have to install a series of expensive pumps and valves, or "dig the system up and start from scratch".
The good news is that advances in our understanding of the way that materials operate now allow us to construct objects beyond traditional silicon-based structures that can be "programmed" to change in response to changes in the external environment, such as an increase in temperature or pressure, for instance.
Of course, to be effective such devices have to be engineered to a high degree of accuracy, in some cases to the nanoscale, which can be very difficult with traditional manufacturing techniques. Yet the high level of accuracy and customisation that the 3D-printing process permits makes it ideal for this purpose.
A boon for healthcare and the Internet of Things
Tibbits thinks that the "basic technological questions around 4D printing have now been largely resolved", so it's now just a case of shifting people's (and companies') perceptions about what is possible, and finding applications. Already, medical-device companies are starting to invest in 4D printing. Tibbits think that this is logical because if 3D printing allows devices to be customised to the current needs of the patient, then 4D printing "will allow the devices to change as the patient's needs evolve". Examples are splints, stents and orthodontic devices that can adapt to changes in a patient's body.
Firms are already starting to invest significant sums in 4D printing. A report produced this summer by Gartner noted that Airbus is now using it to improve the cooling functions of the components in the aeroplanes it manufactures. Briggs Automotive Company is also developing "a morphable wing for its supercar that can adjust to... weather conditions". Perhaps the most ambitious project is the French biotech firm Poietis's use of 4D printing involving cells to produce human tissue. Overall, Gartner predicts that "by 2023, start-up companies working to commercialise 4D printing will attract $300m in venture capital".
Tibbits reckons that the most significant role of 4D printing, and the one that has the greatest commercial potential, is in removing one of the barriers to the mass adoption of "smart" devices. Today most of them need to have additional electronic or robotic elements, to allow them to communicate with each other. Not only is this expensive, but it also makes them larger and bulkier. But if these robotic elements were replaced with special 4D-printed materials, then Tibbits thinks they could be much smaller and lighter.
When looking at 4D printing it's important to be aware that, because this is a very recent technology, it will take longer for it to reach its full commercial potential. Gartner's Basiliere cautions that "mainstream adoption of 4D printing will take more than ten years". Still, he predicts that further scientific advancements in biology, chemistry, electronics and 3D printing "will accelerate the discipline". The future is rapidly approaching.
The stocks to buy now
Stratasys (Nasdaq: SSYS) is probably the purest play on 3D printing available and the company has been involved with the sector for the past three decades, producing award-winning 3D printers and printing systems.
This stock is not for the faint-hearted since the company has struggled to translate its technological leadership into profitability. The stock is still 80% down from its peak five years ago. Nevertheless, Stratasys is finally beginning to reap the financial rewards from years of research, and trades at only a 7% premium to its book value.
Proto Labs (NYSE: PRLB) specialises in rapidly manufacturing custom prototypes and production parts. It has facilities in eight countries, including the US and Britain. It originally focused on injection moulding, but it has become one of the major players in the 3D-printing sector over the last five years, specialising in key production methods and processes, including laser sintering (whereby powered material coalesces into a solid mass thanks to the power of a laser) and stereolithography, the conversion of liquid plastic into solid objects.
Its embrace of 3D printing has enabled it to more than double its sales over the past five years, with customers in a range of sectors from computer electronics to aerospace. All this more than justifies a forward price/earnings (p/e) ratio of 29.
The Swedish engineering company Sandvik AB (Stockholm: SAND) isn't a pure play on 3D printing since it concentrates mainly on metalwork. However, a significant part of its business is now focused on 3D printing and related additive technologies. Earlier this year it made headlines when it created the world's first 3D-printed diamond composite, as well as a smash-proof guitar.
Net profits have doubled over the past five years and the company has a return on capital of more than 20%. Despite this, it still trades at less than 12 times 2020 earnings. It also offers a solid dividend yield of 3.2%.
Another large company investing large amounts of money in 3D printing is Hewlett Packard Enterprise Co (NYSE: HPE). Although Hewlett Packard entered the market relatively recently, it aims to grab a large share of the market for 3D printers by using its expertise with conventional ones to design 3D-models that are cheaper, better quality and more reliable than the competition. Its printers are expensive, with the most advanced model (due next year) costing $400,000. Still, they are already used by big manufacturing companies, including BMW and Volkswagen. The stock is currently cheap, trading on a 2020 p/e of 7.2, with a dividend yield of 3.6%.
While not directly involved in manufacturing itself, Victrex (LSE: VCT) produces polymers used in the production of everything from smartphones to medical devices. It recently developed a special polymer that is particularly suited to 3D printing and also aims to reduce the amount of material wasted during the process. Despite very solid growth of around 8% a year for the last few years, and returns on capital of more than 20%, it is still valued at only 16 times 2020 earnings. It also pays a dividend yield of 3.2%.
Matthew graduated from the University of Durham in 2004; he then gained an MSc, followed by a PhD at the London School of Economics.
He has previously written for a wide range of publications, including the Guardian and the Economist, and also helped to run a newsletter on terrorism. He has spent time at Lehman Brothers, Citigroup and the consultancy Lombard Street Research.
Matthew is the author of Superinvestors: Lessons from the greatest investors in history, published by Harriman House, which has been translated into several languages. His second book, Investing Explained: The Accessible Guide to Building an Investment Portfolio, is published by Kogan Page.
As senior writer, he writes the shares and politics & economics pages, as well as weekly Blowing It and Great Frauds in History columns He also writes a fortnightly reviews page and trading tips, as well as regular cover stories and multi-page investment focus features.
Follow Matthew on Twitter: @DrMatthewPartri
-
Meta’s AI splurge rattles investors
Meta's decision to join the AI race is driving investors away
By Dr Matthew Partridge Published
-
Is it a good time to invest in the UK?
Temple Bar Investment Trust is a diversified bet on British equities and looks excellent value, says Max King
By Max King Published
-
Invest in space: the final frontier for investors
Cover Story Matthew Partridge takes a look at how to invest in space, and explores the top stocks to buy to build exposure to this rapidly expanding sector.
By Dr Matthew Partridge Published
-
Invest in Brazil as the country gets set for growth
Cover Story It’s time to invest in Brazil as the economic powerhouse looks set to profit from the two key trends of the next 20 years: the global energy transition and population growth, says James McKeigue.
By James McKeigue Published
-
5 of the world’s best stocks
Cover Story Here are five of the world’s best stocks according to Rupert Hargreaves. He believes all of these businesses have unique advantages that will help them grow.
By Rupert Hargreaves Published
-
The best British tech stocks from a thriving sector
Cover Story Move over, Silicon Valley. Over the past two decades the UK has become one of the main global hubs for tech start-ups. Matthew Partridge explains why, and highlights the most promising investments.
By Dr Matthew Partridge Published
-
Could gold be the basis for a new global currency?
Cover Story Gold has always been the most reliable form of money. Now collaboration between China and Russia could lead to a new gold-backed means of exchange – giving prices a big boost, says Dominic Frisby
By Dominic Frisby Published
-
How to invest in videogames – a Great British success story
Cover Story The pandemic gave the videogame sector a big boost, and that strong growth will endure. Bruce Packard provides an overview of the global outlook and assesses the four key UK-listed gaming firms.
By Bruce Packard Published
-
How to invest in smart factories as the “fourth industrial revolution” arrives
Cover Story Exciting new technologies and trends are coming together to change the face of manufacturing. Matthew Partridge looks at the companies that will drive the fourth industrial revolution.
By Dr Matthew Partridge Published
-
Why now is a good time to buy diamond miners
Cover Story Demand for the gems is set to outstrip supply, making it a good time to buy miners, says David J. Stevenson.
By David J Stevenson Last updated